MECACONCEPT,
INDUSTRIAL ROBOTICS SOLUTIONS

From the simplest application to the most complex trajectory studies, MECACONCEPT supports you in the realization of your robotic projects.
ROBOTIC PALLETIZING SYSTEM
WHY AUTOMATE PALLETIZING?
Robotic palletizing offers a number of advantages, including
- reduction of RSI by limiting manual and repetitive handling of loads
- increased throughput
- optimization of the logistics process during loading operations.
AUTOMATED PALLETIZING : COBOT OR ROBOT?
Palletizing is the organized arrangement of stackable shapes. The palletizing operation therefore consists in arranging objects in successive layers in a secure and stable manner.
However, each palletizing application is specific to the company. Here are the main criteria to consider before opting for a cobotic or robotic island solution:
- characteristics of the objects to be handled: size, weight, shape
- production rate
- pallet or support dimensions (European pallets, half-pallets, etc.)
- working environment (wet, grey areas, etc.)
- integration into upstream/downstream process
- presence of operators in the immediate vicinity
The functional and risk analyses carried out by the robotic integrator will guide the technical choices towards the most appropriate solution.
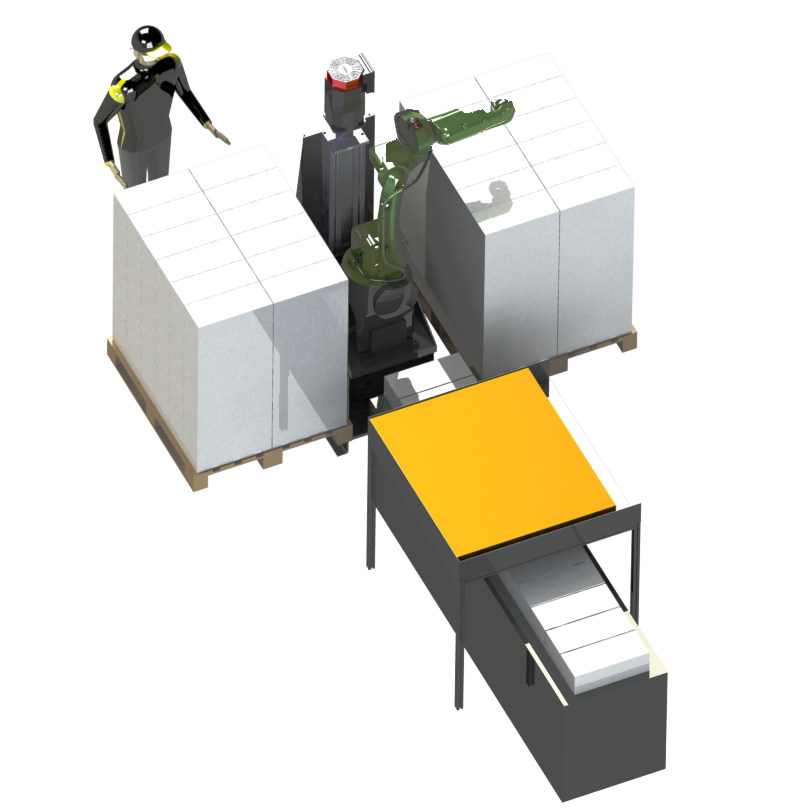
palletizing by collaborative robot
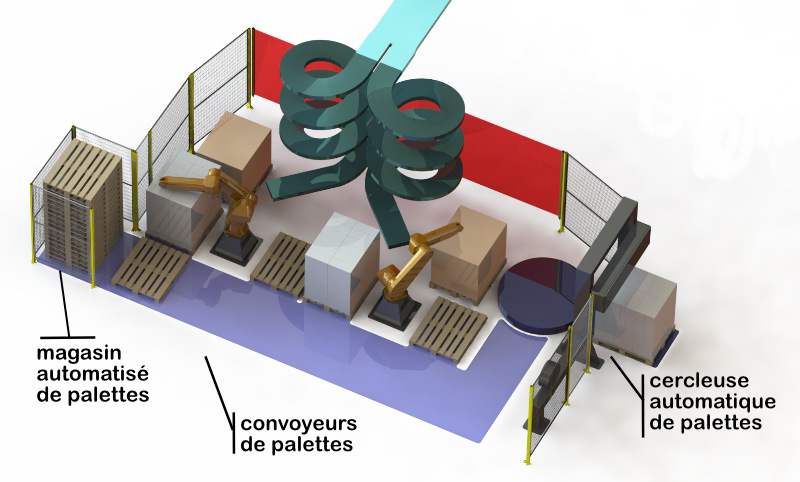
General layout study: robotized palletizing island, integration of additional equipment and automated management of upstream/downstream flows
MACHINE LOADING/UNLOADING ROBOT
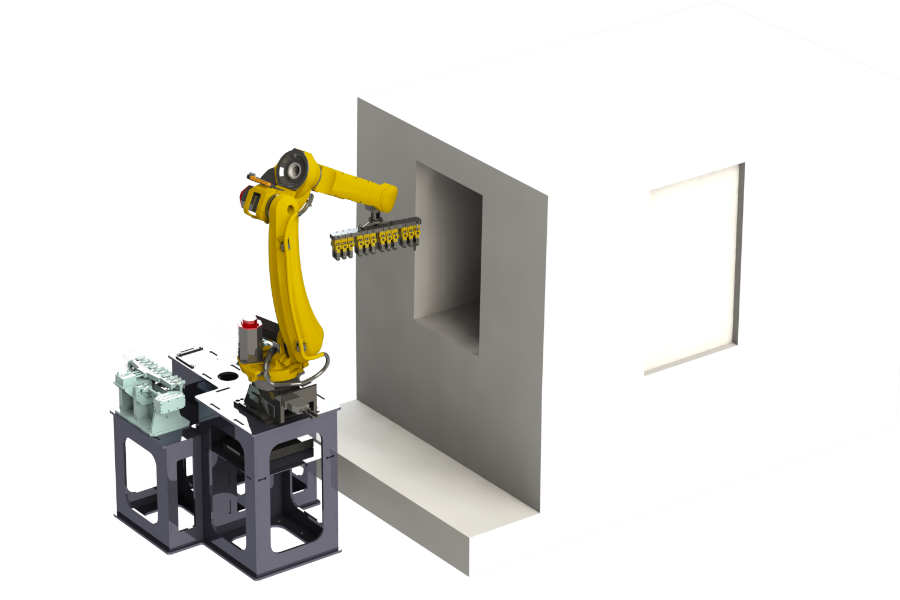
ROBOTIZED LOADING FOR MACHINING CENTERS
Automated loading/unloading of machines makes it possible to :
- relieve operators of repetitive, tedious tasks with no real added value.
- respond to increased production rates (implementation of 3 X 8), even on a one-off basis.
Depending on the cycle diagram and the configuration of the work area, the same robot can feed one or more machines. In addition, to facilitate the production of specific small batches, simplified and secure operator access to the machining centers must be offered and managed.
PICK AND PLACE
EXAMPLE OF A PICK AND PLACE ROBOTIZED APPLICATION
On-the-fly collection (pick & place) of parts placed on a conveyor by a robot, and placement on specific pick & place modules.
TECHNOLOGIES USED :
- 2D vision
- SCARA robot / Delta robot
Good to know: Possibility of using the vision system supplied by the robot manufacturer, but also development of customized solutions from the range of systems available: autonomous 2D/3D sensor or PC-based system.
ROBOTIZED PACKAGING CELL
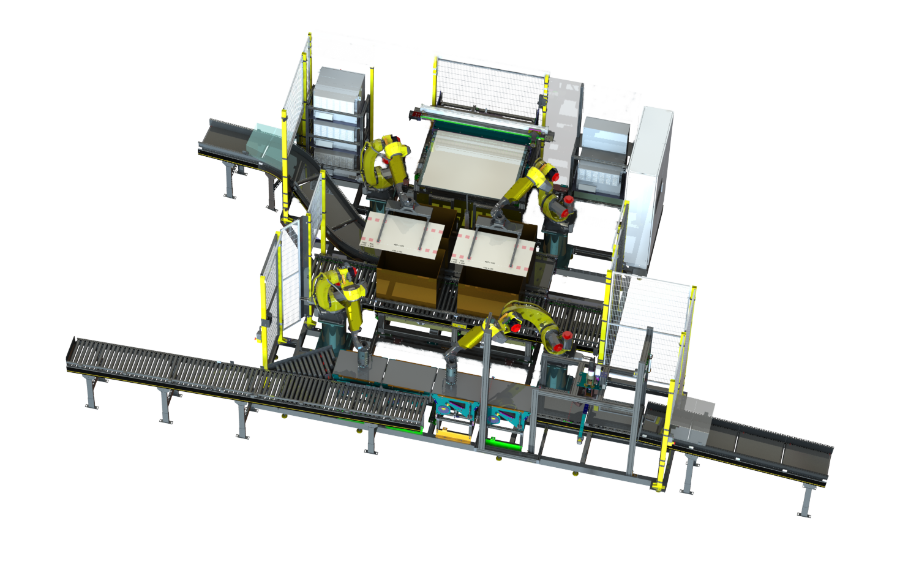
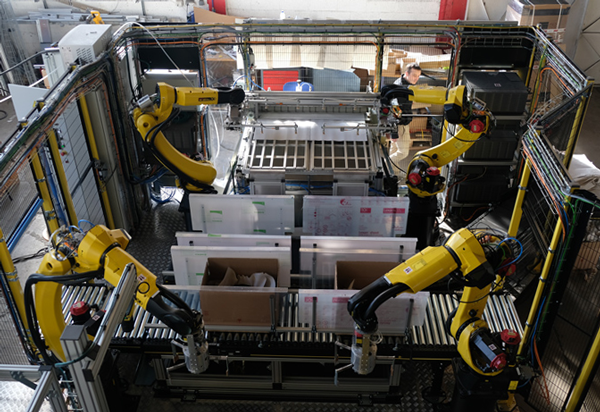
DESCRIPTION :
End-of-line robotized packing of multi-reference products into cartons and insertion of interleaves.
TECHNOLOGIES USED :
Robots synchronized 2 by 2
- Differentiated management of case packing plans according to production campaigns
- Development of a vision system with linear camera acquisition and barcode readers for product identification and positioning.
- Automated control of the robotized cell
Good to know: During the pre-project phase, the cycle diagram can be validated using a flow simulation study (carried out with Tecnomatix® Plant Simulation).
SPECIFIC APPLICATION DEVELOPMENT
Example: process robot with complex trajectory tracking
- Design and production of the robot cell integrating a heavy-duty robot
- Design of the specific machining head
- Assistance in generating complex machining trajectories using in-house CAM software
- Management of 9 robot axes, including 1 machining axis and 2 interpolated rotary axes
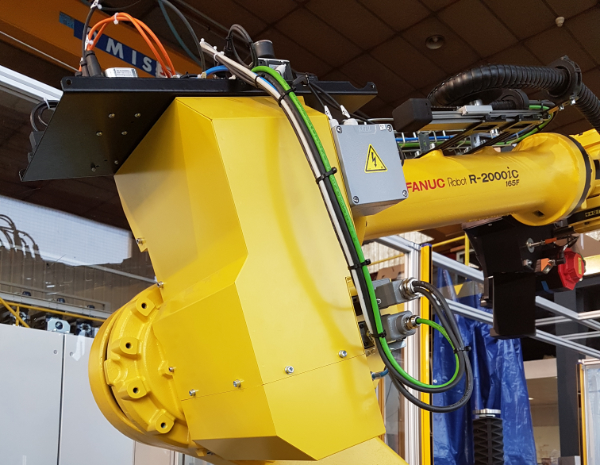
Mobile Manipulator ROBOT
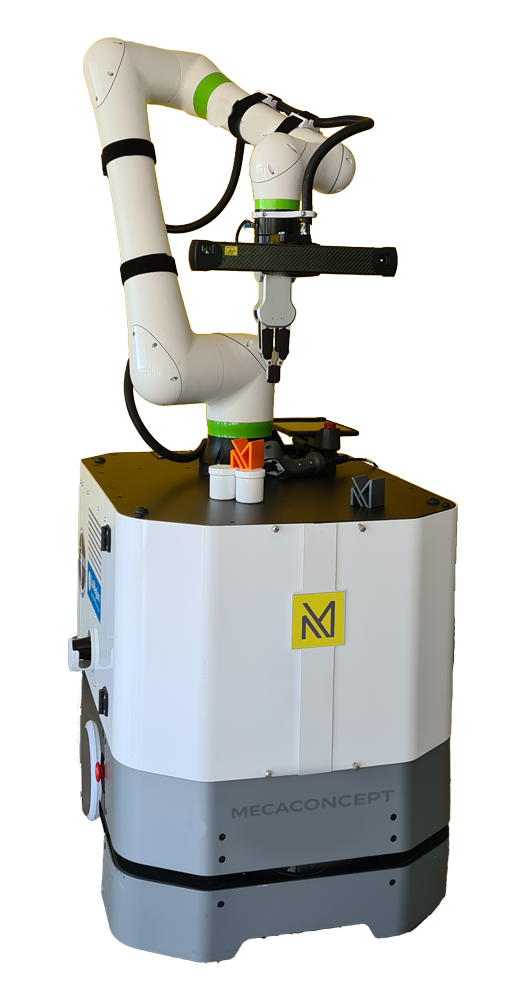
Towards a new generation of Mobile Manipulator Robot (MoMas)capable of carrying out different missions at different locations in a workshop, factory or building. The Mobile Assistant Robot combines the power of image processing algorithms with the mobility and agility of mobile and collaborative robotics. It's a set of technological bricks that can be combined and upgraded according to customer needs.
Various interfacing protocols enable the robot's actions to be coordinated with the various players involved (machines/line operator/operators).
- machine loading and unloading
- spot sampling on line
- Intralogistics: picking or handling of parts
- specific processes (autonomous sanding, quality control, defect inspection, etc.)
A WORD FROM THE EXPERT
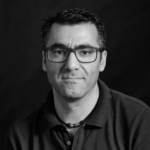
"The Mobile Assistant Robot is designed to be fully customizable to customer specifications. Its development is based on particularly robust image processing and decision-making algorithms."
Why entrust us with your industrial development projects?
MECACONCEPT

- 31 years' experience in industrial project management
- the expertise of a multidisciplinary team: mechanical engineers, automation specialists, robotics specialists, IT specialists
- major references in cutting-edge industries
OUR BUSINESS :INDUSTRIAL ENGINEERING
- mechanical design office
- automation
- robotics
- special machine builder
- industrial IT development
- industrial vision integrator